First Push at ACO
Otto Simon Ltd • September 5, 2016
Battery 3 of the Appleby Coke Ovens (ACO) at Scunthorpe, is back in business!
The first push of the newly restored battery was conducted in late July after an extensive recovery project which included the replacement of all 33 oven door frames, pulman valves and ascension pipe assemblies, and service pipework. In addition to this, several end flue repairs and extensive ceramic welding of the oven refractory was carried out.
The project took more than 250,000 man-hours to complete and was achieved whilst working between 2 live batteries with minimal disruption to normal operations; which enabled continued production of coke for British Steel’s blast furnaces.
The battery had been steadily declining in its ability to produce coke and gas, and was struggling to produce enough coke to sustain the blast furnaces. In December 2015 the decision was made to ‘Hot Idle’ the battery (hold the battery at a temperature of 950°C while the work was carried out) and repair works commenced in January 2016.
Otto Simon carried out the majority of the project, acting as Principal Contractor under CDM 2015. Nick Shaw, Otto Simons’ Head of Coke, Construction and Commissioning said: “It’s been a pleasure to work with British Steel on this project. We forged a strong and productive working relationship to make sure the project was delivered safely and on time. Despite challenges of working between operational batteries, a tremendous amount of effort and engineering has gone into bringing battery 3 back into production with a greatly improved environmental performance."
Otto Simon’s hard work and the coordination between project teams has been praised by British Steel’s Recovery Team Leaders, Chris Peill and Dale Cryer. Dale said "Every single person involved in the project should feel proud with what we've achieved”, with Chris commenting: “There was fantastic cooperation between production teams and the rebuild contractors to get the project finished on time.”
Thanks to the recovery project, the plant’s production volume of coke has almost doubled from 4.5kt to approximately 9kt. Jim Worsely, Plant Manager ACO said: “The combined benefit of coke and gas production from battery 3 will be approximately £12m year on year. ACO has had a very challenging but productive 12 months. Delivering a 50% improvement in our safety performance along with nearly doubling the plant output is an incredible achievement. The team at ACO has a lot to be proud of."
The project was not without its difficulties. Working between two live ovens provided numerous health and safety risks which were expertly managed during the project thanks to the additional control measures put in place. "During this phenomenal project, the only 'injury’ we had was a small blood blister, which is absolutely incredible and shows how dedicated the guys were," said Jim. The additional measures put in place for this project are now being rolled out across the rest of ACO’s operations.
Jon Campbell, ACO Recovery Manager told Steel Matters, British Steel’s in-house magazine: "It gives me great pleasure to see the end of the phase of battery 3. It's personally been one of the most difficult challenges - to make sure a project, a live recovery and the prime manufacturing process was planned in such a way that all parties achieved their goals."
The project was a huge success for all involved and shows a commitment to the future of the Scunthorpe site. British Steel will now start to look at repair works for Batteries 1,2 and 4. Otto Simon was delighted to work alongside British Steel on this project, and is looking forward to further collaborations on this site in the future.
Back to Blog
Show More
Recent Blog Posts
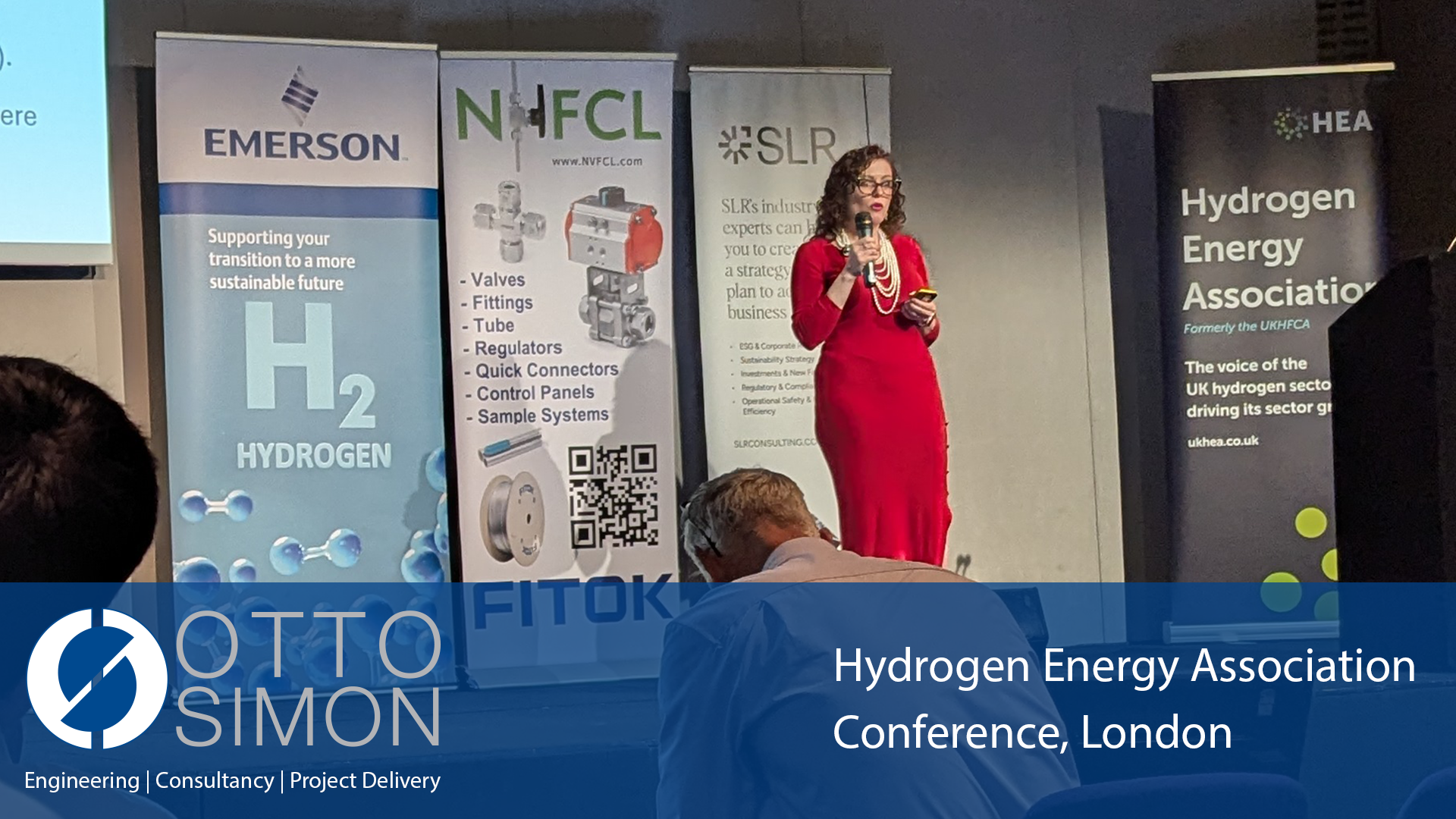
Otto Simon recently attended the Hydrogen Energy Association (HEA) annual conference in Westminster, London, a key event for the hydrogen industry. The conference featured a keynote speech by Sarah Jones, UK Government Minister of State for Industry and Net Zero , highlighting the government's commitment to this crucial sector. Our team had the invaluable opportunity to hear directly from industry-leading hydrogen experts , gaining first-hand insights into the latest policies and government funding initiatives. This direct access to information is vital for staying at the forefront of hydrogen advancements. Congratulations to Clive Mansfield and Clare Dunkerley from our team, who actively participated in the networking sessions, engaging in discussions about hydrogen and safety —a critical aspect of our work. They also gathered useful information that will directly benefit our ongoing hydrogen projects.
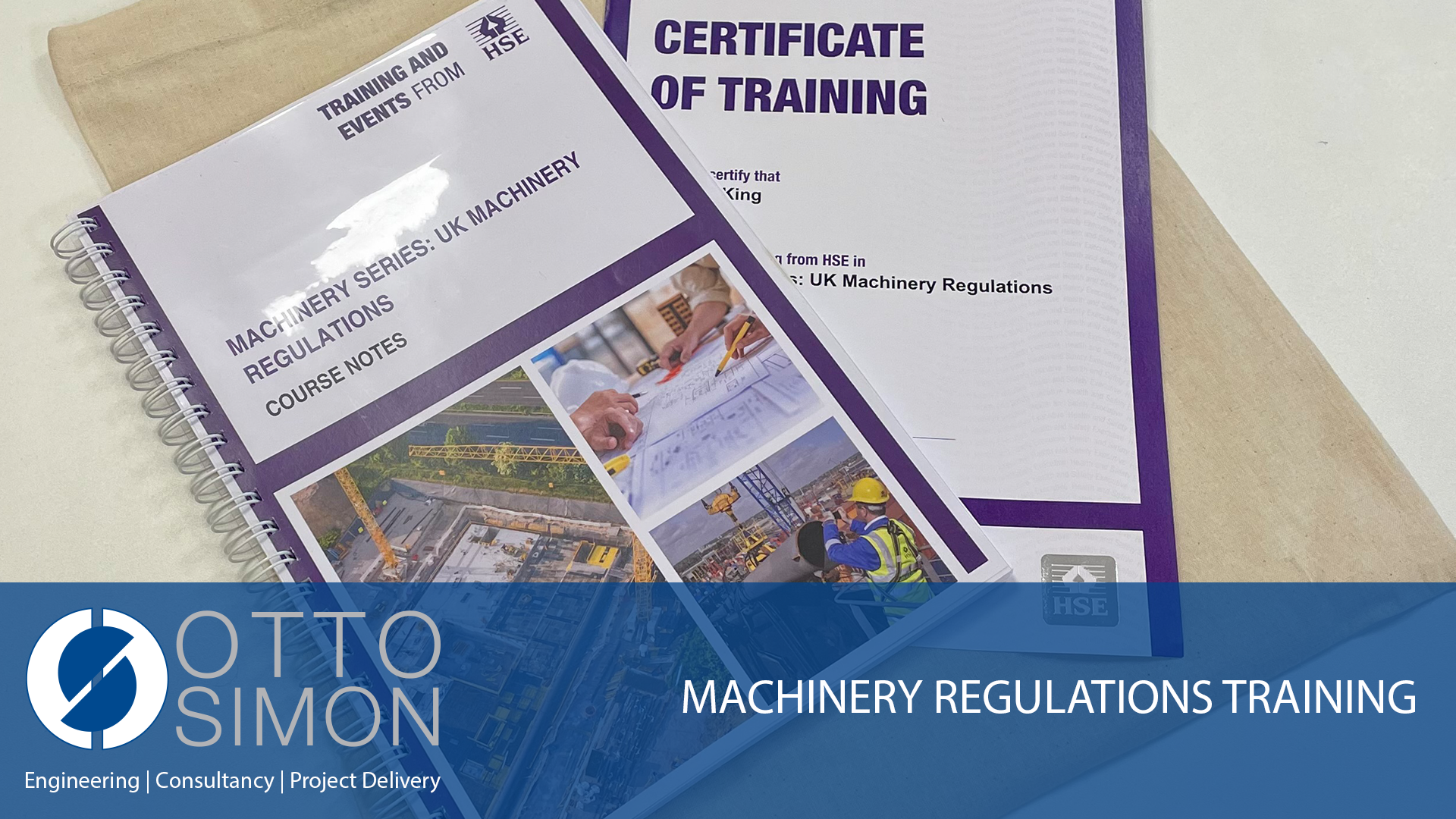
Here at Otto Simon, we're committed to staying at the forefront of safety and compliance in Process Plant projects. That's why two of our seasoned principal engineers, Mike Wray and Mike Westerman, recently attended a crucial refresher course on machinery regulations at the HSE Science and Research Centre. In the world of Process Plant projects, it's common to encounter machinery assemblies where vendors don't provide a declaration of conformity. With the recent publication of the new EU Machinery Regulation 2023/1230/EU, it's more important than ever to be on top of the latest guidelines. This ensures we can continue to offer our UK-based clients the best advice on their responsibilities and how to apply conformity assessments when machinery risks are present. This applies to both new equipment and the repurposing of existing machinery. Considering there are over 800 standards related to machinery design, our approach is meticulous. We utilise a thorough hazard identification process to carefully evaluate risks and implement best practice safety mitigations in all our designs. This proactive approach helps us ensure the highest level of safety for your projects. Please get in touch for assistance.

Prime Minister, Kier Starmer visits St Helens, Merseyside today as he paid a visit to the Glass Futures facility! The Prime Minister spoke to workers at the facility this morning, Thursday, May 29 during a visit. “Can I just start by thanking those that work here for showing me this morning what you do, showing me the skills that you have, telling me a bit about what goes on here and the incredible history. “If I’ve understood what you’ve told me glass has been made on this very site for the best part of 250 years." “I think Pilkington may have been running the business before, and we can actually just see Pilkington out there so for you to be continuing with Glass Futures, very apt name, working here is fantastic and I can see how proud you are of what you do, each of you contributing with your different skills to what is happening here." The Labour politician added: “As I’ve said many, many, times you can read a briefing in London or you can come and see the workforce and come and see the people with the real skills and understand what they’re doing and thank you for allowing me to do the second of those as I’ve got a really good sense of what you’re doing here, how you’re doing it and the incredible way you’re doing it, each of you contributing in your own way and I can see that pride.” The £54m innovative research and technology facility was opened in Peasley Cross in 2023, at the former United Glass site. The mission is to help decarbonise the global glass industry by pioneering ways of making carbon-neutral glass.